Mecha break maintenance is an essential practice for anyone who relies on heavy machinery in their daily operations. Whether you're managing a construction site, a manufacturing plant, or even a home workshop, ensuring that your machines are well-maintained can save you time, money, and frustration. Regular maintenance not only extends the lifespan of your equipment but also enhances safety and efficiency. In this article, we will explore the ins and outs of mecha break maintenance, providing you with the knowledge and tools to keep your machines running smoothly.
Mechanical breakdowns can be costly and disruptive, often leading to downtime that affects productivity and profitability. By understanding the principles of mecha break maintenance, you can prevent these issues before they arise. This guide will walk you through the best practices, common pitfalls, and expert tips to ensure your machinery remains in peak condition. We'll also delve into the importance of regular inspections, the role of lubrication, and how to troubleshoot common problems.
As we navigate through this comprehensive guide, you'll gain insights from industry experts and learn about the latest advancements in maintenance technology. Whether you're a seasoned professional or a newcomer to the field, this article aims to equip you with the knowledge to make informed decisions about your machinery. So, let's dive in and explore the world of mecha break maintenance, ensuring that your equipment remains reliable and efficient for years to come.
Read also:Tamil Big Boops A Comprehensive Guide To Understanding And Appreciating Tamil Cinema
Table of Contents
- Introduction to Mecha Break Maintenance
- Importance of Regular Maintenance
- Common Causes of Mechanical Breakdowns
- Essential Maintenance Practices
- Advanced Maintenance Techniques
- Troubleshooting Common Problems
- Tools and Equipment for Maintenance
- The Role of Technology in Maintenance
- Safety Measures During Maintenance
- Conclusion and Call to Action
Introduction to Mecha Break Maintenance
Mecha break maintenance refers to the systematic process of inspecting, servicing, and repairing machinery to prevent unexpected breakdowns. This proactive approach is crucial for maintaining the efficiency and reliability of mechanical systems. By addressing potential issues before they escalate, mecha break maintenance helps reduce downtime and extend the lifespan of equipment.
The concept of mecha break maintenance is rooted in the understanding that machinery, like any other tool, requires regular care to function optimally. Neglecting maintenance can lead to costly repairs, safety hazards, and decreased productivity. Therefore, implementing a structured maintenance plan is vital for any business that relies on mechanical equipment.
Throughout this section, we will explore the fundamental principles of mecha break maintenance, highlighting its benefits and the key components involved. By the end, you'll have a solid foundation to build upon as we delve deeper into the specifics of maintaining various types of machinery.
Importance of Regular Maintenance
Regular maintenance is the backbone of mecha break maintenance. It involves routine checks and servicing to ensure that machinery operates at its best. This section will discuss why regular maintenance is crucial and how it can impact your operations.
One of the primary benefits of regular maintenance is the prevention of unexpected breakdowns. By identifying and addressing minor issues early, you can avoid major repairs that could disrupt your workflow. Additionally, well-maintained machinery tends to operate more efficiently, reducing energy consumption and operational costs.
Moreover, regular maintenance enhances safety in the workplace. Faulty equipment can pose significant risks to operators and other personnel. By adhering to a strict maintenance schedule, you can minimize these risks and create a safer working environment. In the following sections, we will explore specific maintenance practices that contribute to these benefits.
Read also:Icon Pop Quiz A Fun And Engaging Way To Test Your Knowledge
Common Causes of Mechanical Breakdowns
Understanding the common causes of mechanical breakdowns is essential for effective mecha break maintenance. This section will outline the primary factors that contribute to equipment failure and how to mitigate them.
One of the leading causes of mechanical breakdowns is wear and tear. Over time, components such as belts, gears, and bearings can degrade, leading to reduced performance and eventual failure. Regular inspections and timely replacements are crucial to preventing these issues.
Another common cause is inadequate lubrication. Lubricants reduce friction between moving parts, preventing overheating and wear. Neglecting to lubricate machinery can result in increased friction, leading to breakdowns. We will discuss the importance of lubrication in more detail in the next section.
Lastly, environmental factors such as temperature fluctuations and exposure to dust and debris can also contribute to mechanical failures. Implementing protective measures, such as using covers and seals, can help safeguard machinery against these elements.
Essential Maintenance Practices
Maintaining machinery involves a combination of routine practices that ensure optimal performance. In this section, we will explore some of the essential maintenance practices that should be part of your mecha break maintenance strategy.
Routine Inspections
Routine inspections are the first line of defense against mechanical breakdowns. These inspections involve checking various components of the machinery for signs of wear, damage, or malfunction. By conducting regular inspections, you can identify potential issues before they escalate into major problems.
During inspections, pay close attention to critical components such as belts, gears, and bearings. Look for signs of wear, such as cracks, fraying, or excessive play. Additionally, check for leaks in hydraulic systems and ensure that all fasteners are securely tightened.
Documenting inspection findings is also important. Keeping a detailed log of inspections and maintenance activities can help track the condition of your machinery over time. This information can be invaluable for identifying patterns and making informed decisions about future maintenance needs.
Lubrication and Cleaning
Lubrication is a critical aspect of mecha break maintenance. Proper lubrication reduces friction between moving parts, preventing overheating and wear. It also helps to dissipate heat and protect components from corrosion.
When lubricating machinery, it's essential to use the correct type and amount of lubricant. Different machines and components may require specific lubricants, so always refer to the manufacturer's recommendations. Over-lubrication can be just as harmful as under-lubrication, leading to excess buildup and potential damage.
Cleaning is another vital practice in maintaining machinery. Dust, dirt, and debris can accumulate on equipment, leading to increased wear and reduced performance. Regularly cleaning machinery helps prevent these issues and ensures that components function smoothly. Use appropriate cleaning agents and methods to avoid damaging sensitive parts.
Advanced Maintenance Techniques
In addition to routine practices, advanced maintenance techniques can further enhance the reliability and efficiency of your machinery. This section will explore some of these techniques and their benefits.
Predictive maintenance is an advanced technique that uses data and analytics to predict when equipment is likely to fail. By monitoring key performance indicators and analyzing trends, you can schedule maintenance activities proactively, reducing the risk of unexpected breakdowns.
Condition-based maintenance is another technique that involves monitoring the actual condition of machinery to determine maintenance needs. This approach relies on sensors and diagnostic tools to assess the health of components in real-time. By addressing issues based on actual conditions rather than predetermined schedules, you can optimize maintenance efforts and reduce costs.
Implementing these advanced techniques requires investment in technology and training. However, the long-term benefits, including increased uptime and reduced maintenance costs, make them worthwhile considerations for any operation.
Troubleshooting Common Problems
Despite regular maintenance, mechanical issues can still arise. Knowing how to troubleshoot common problems is essential for minimizing downtime and restoring operations quickly. This section will provide guidance on diagnosing and resolving typical issues.
One common problem is overheating. Overheating can be caused by inadequate lubrication, blocked cooling systems, or excessive friction. To address this, check lubrication levels, inspect cooling systems for blockages, and ensure that components are properly aligned.
Another frequent issue is unusual noises or vibrations. These symptoms can indicate misalignment, worn bearings, or loose components. Conduct a thorough inspection to identify the source of the problem and make necessary adjustments or replacements.
Electrical issues can also cause machinery to malfunction. Check wiring connections, fuses, and circuit breakers to ensure that electrical systems are functioning correctly. If you're unsure about electrical troubleshooting, it's best to consult a qualified technician.
Tools and Equipment for Maintenance
Having the right tools and equipment is crucial for effective mecha break maintenance. This section will outline some of the essential tools you'll need to perform maintenance tasks efficiently.
Basic hand tools, such as wrenches, screwdrivers, and pliers, are indispensable for most maintenance activities. Additionally, specialized tools like torque wrenches and pullers may be required for specific tasks. Investing in high-quality tools ensures that you can perform maintenance accurately and safely.
Diagnostic tools are also important for troubleshooting and condition monitoring. Multimeters, infrared thermometers, and vibration analyzers can help identify issues and assess the condition of machinery. These tools provide valuable insights that can guide maintenance decisions.
Lastly, having a well-organized tool storage system is essential for maintaining efficiency. Keeping tools organized and easily accessible reduces the time spent searching for the right tool and minimizes the risk of losing or damaging equipment.
The Role of Technology in Maintenance
Technology plays a significant role in modern mecha break maintenance. Advances in digital tools and automation have transformed the way maintenance is performed, offering new opportunities for efficiency and reliability.
One of the most impactful technological advancements is the use of Internet of Things (IoT) devices. IoT sensors can monitor machinery in real-time, providing data on performance, temperature, and other critical parameters. This data can be analyzed to predict potential issues and optimize maintenance schedules.
Automation is another area where technology is making a difference. Automated maintenance systems can perform routine tasks such as lubrication and inspections, reducing the need for manual intervention. This not only improves efficiency but also enhances safety by minimizing human exposure to hazardous environments.
Software solutions, such as computerized maintenance management systems (CMMS), are also valuable tools for managing maintenance activities. These systems help track maintenance schedules, document inspections, and generate reports, providing a comprehensive overview of maintenance operations.
Safety Measures During Maintenance
Safety should always be a top priority during mecha break maintenance. This section will outline essential safety measures to protect both personnel and equipment during maintenance activities.
Before starting any maintenance task, ensure that machinery is properly shut down and isolated from power sources. Lockout/tagout procedures are critical for preventing accidental startups. Always follow manufacturer guidelines and safety protocols when performing maintenance.
Personal protective equipment (PPE) is essential for safeguarding personnel. Depending on the task, this may include gloves, safety glasses, helmets, and ear protection. Ensure that all team members are trained in the proper use of PPE and understand the risks associated with maintenance activities.
Additionally, maintaining a clean and organized work environment is crucial for safety. Remove any obstacles or hazards from the work area and ensure that tools and equipment are stored properly. Regular safety audits and training sessions can help reinforce best practices and keep safety top of mind.
Conclusion and Call to Action
In conclusion, mecha break maintenance is an essential practice for ensuring the reliability and efficiency of machinery. By implementing regular maintenance routines, understanding common causes of breakdowns, and utilizing advanced techniques, you can prevent costly repairs and downtime.
We've explored various aspects of mecha break maintenance, from routine inspections and lubrication to advanced predictive techniques and the role of technology. By following these best practices, you can extend the lifespan of your equipment and enhance safety in your operations.
We encourage you to apply the knowledge gained from this guide to your maintenance strategies. Share your experiences and insights with others in the industry, and don't hesitate to reach out for expert advice when needed. Together, we can build a community of informed and proactive maintenance professionals dedicated to keeping machinery in top condition.
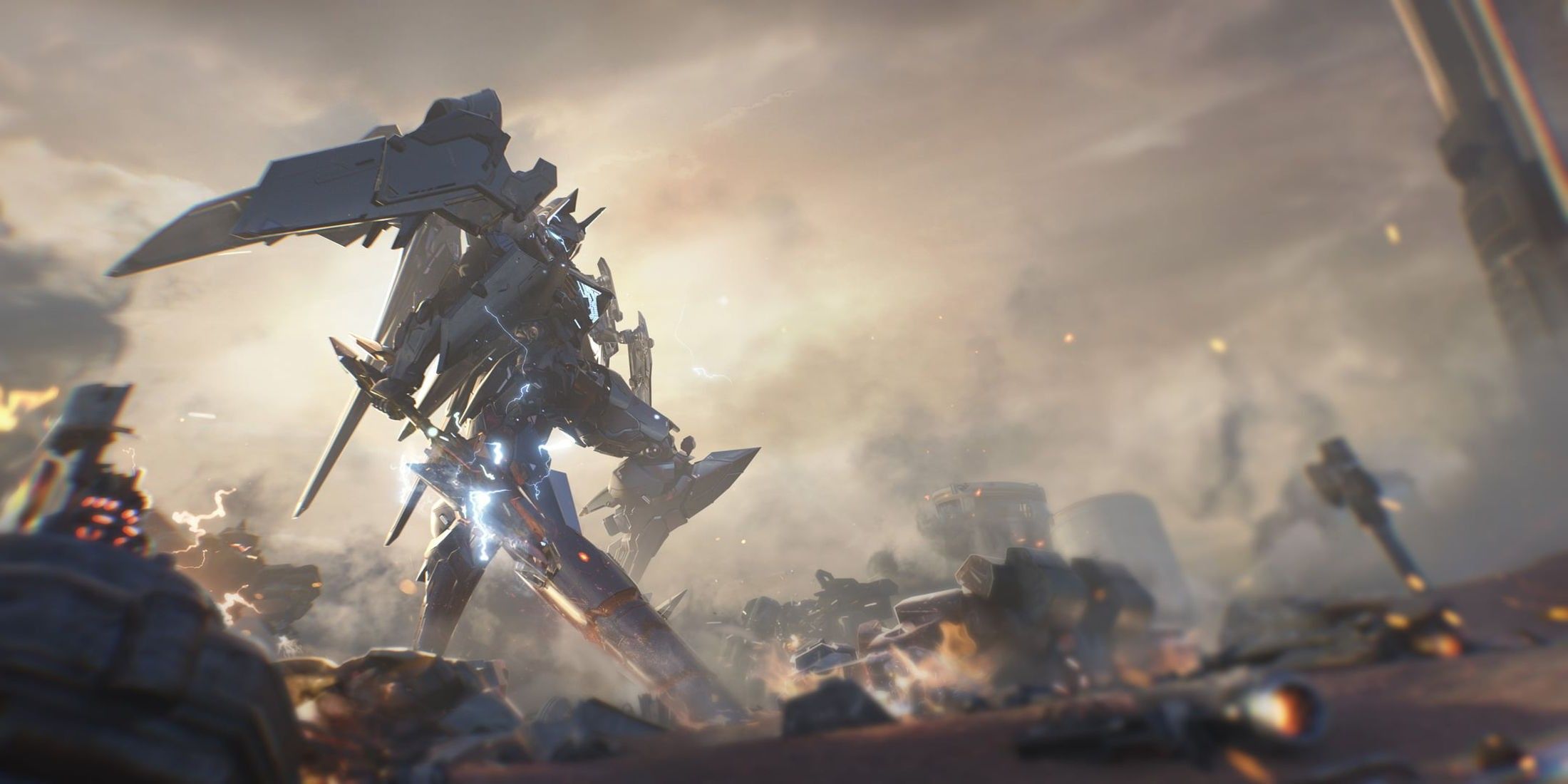
