Defects Per Million Opportunities (DPMO) is a critical metric used in quality management and process improvement, particularly in Six Sigma methodologies. It measures the number of defects per one million opportunities, offering a standardized way to evaluate process performance. Whether you're a business owner, a quality control professional, or someone looking to improve operational efficiency, understanding DPMO is essential for achieving excellence in any process. This article dives deep into the meaning, calculation, and applications of DPMO, ensuring you have all the tools you need to leverage this powerful metric.
As businesses strive to deliver high-quality products and services, metrics like DPMO become indispensable. By quantifying defects and opportunities, organizations can identify areas for improvement, reduce errors, and enhance customer satisfaction. In this guide, we’ll explore the nuances of DPMO, its significance in various industries, and how it aligns with broader quality management frameworks like Six Sigma. Whether you're new to the concept or looking to refine your understanding, this article will provide valuable insights to help you achieve operational excellence.
Understanding DPMO is not just about crunching numbers—it’s about transforming data into actionable insights. By the end of this article, you’ll have a clear understanding of what DPMO is, how it’s calculated, and how it can be applied to real-world scenarios. We’ll also discuss its role in improving business processes, ensuring compliance with industry standards, and driving continuous improvement. Let’s dive into the details and unlock the potential of DPMO to elevate your quality management practices.
Read also:Vintage Stag Films A Fascinating Dive Into Early Erotic Cinema
Table of Contents
- What is DPMO?
- How to Calculate DPMO
- The Importance of DPMO in Quality Management
- DPMO in Six Sigma Methodologies
- Real-World Applications of DPMO
- Common Misconceptions About DPMO
- Tools and Software for Calculating DPMO
- Challenges in Implementing DPMO
- Case Studies: Success Stories Using DPMO
- Conclusion and Key Takeaways
What is DPMO?
Defects Per Million Opportunities (DPMO) is a statistical measure used to evaluate the quality and performance of a process. It quantifies the number of defects that occur in a process per one million opportunities. This metric is particularly valuable because it provides a standardized way to compare the performance of different processes, regardless of their scale or complexity.
To break it down further:
- Defects: Any deviation from the desired outcome or specification in a process.
- Opportunities: The total number of chances for a defect to occur in a process.
For example, in a manufacturing process, if a product has 10 components, each component represents an opportunity for a defect. If 100 products are produced, there are 1,000 opportunities for defects (10 components x 100 products). If 5 defects are identified, the DPMO can be calculated to assess the process's performance.
Why DPMO Matters
DPMO is more than just a number—it’s a reflection of a process’s efficiency and reliability. By measuring DPMO, organizations can:
- Identify areas for improvement.
- Set benchmarks for quality performance.
- Track progress over time.
How to Calculate DPMO
Calculating DPMO is straightforward, but it requires accurate data collection and a clear understanding of the process. The formula for DPMO is:
DPMO = (Number of Defects / (Number of Units x Number of Opportunities per Unit)) x 1,000,000
Read also:Jamie Tartt Hair Unveiling The Secrets Behind The Iconic Look
Step-by-Step Guide to Calculating DPMO
- Determine the Number of Defects: Count the total number of defects identified in the process.
- Calculate the Number of Opportunities: Multiply the number of units produced by the number of opportunities for defects per unit.
- Plug Values into the Formula: Use the DPMO formula to compute the metric.
For instance, if a process produces 500 units, each with 20 opportunities for defects, and 50 defects are identified, the DPMO would be:
DPMO = (50 / (500 x 20)) x 1,000,000 = 5,000
The Importance of DPMO in Quality Management
DPMO plays a pivotal role in quality management frameworks like Six Sigma. It serves as a benchmark for evaluating process performance and identifying areas for improvement. Here’s why DPMO is so important:
- Standardization: DPMO provides a universal metric that allows organizations to compare the performance of different processes.
- Continuous Improvement: By tracking DPMO over time, organizations can measure the impact of process improvements.
- Customer Satisfaction: Lower DPMO values indicate fewer defects, which directly translates to higher customer satisfaction.
Applications Across Industries
DPMO is not limited to manufacturing—it’s widely used in healthcare, finance, software development, and more. For example:
- In healthcare, DPMO can measure errors in patient care processes.
- In software development, it can track bugs or defects in code.
DPMO in Six Sigma Methodologies
Six Sigma is a data-driven methodology aimed at reducing defects and improving process efficiency. DPMO is a cornerstone of Six Sigma, as it quantifies the level of process performance and helps organizations achieve their Six Sigma goals.
Six Sigma Levels and DPMO
Six Sigma defines process performance in terms of "sigma levels," each corresponding to a specific DPMO value:
- 1 Sigma: 690,000 DPMO
- 2 Sigma: 308,000 DPMO
- 3 Sigma: 66,800 DPMO
- 4 Sigma: 6,210 DPMO
- 5 Sigma: 233 DPMO
- 6 Sigma: 3.4 DPMO
Achieving Six Sigma (3.4 DPMO) is the ultimate goal, as it represents near-perfect process performance.
Real-World Applications of DPMO
DPMO is widely used across industries to drive quality improvements. Here are some real-world examples:
Manufacturing
In manufacturing, DPMO helps identify defects in production lines, enabling organizations to reduce waste and improve product quality.
Healthcare
Hospitals use DPMO to measure errors in patient care processes, such as medication administration or surgical procedures.
Software Development
Software companies use DPMO to track bugs and defects in code, ensuring higher-quality software releases.
Common Misconceptions About DPMO
Despite its widespread use, there are several misconceptions about DPMO:
- Myth 1: DPMO is only relevant for manufacturing. In reality, it applies to any process with measurable opportunities and defects.
- Myth 2: Lower DPMO always means better performance. While lower DPMO is desirable, it’s essential to consider the context and specific goals of the process.
Tools and Software for Calculating DPMO
Several tools and software solutions can help organizations calculate and track DPMO:
- Minitab: A statistical software widely used in Six Sigma projects.
- Excel: Simple spreadsheets can be used to calculate DPMO manually.
- QI Macros: An Excel add-in designed for quality improvement projects.
Challenges in Implementing DPMO
While DPMO is a powerful metric, implementing it effectively can be challenging:
- Data Collection: Accurate data is essential for calculating DPMO.
- Defining Opportunities: Identifying and defining opportunities for defects can be complex.
Case Studies: Success Stories Using DPMO
Many organizations have successfully used DPMO to drive quality improvements. For example:
- General Electric: GE’s Six Sigma initiatives, which rely heavily on DPMO, have saved billions of dollars.
- Toyota: Toyota’s lean manufacturing processes use DPMO to maintain high-quality standards.
Conclusion and Key Takeaways
Defects Per Million Opportunities (DPMO) is a powerful metric for evaluating process performance and driving quality improvements. By understanding and applying DPMO, organizations can identify areas for improvement, set benchmarks, and achieve operational excellence.
To recap:
- DPMO measures defects per one million opportunities, providing a standardized way to evaluate process performance.
- It is a cornerstone of Six Sigma methodologies and is widely used across industries.
- Accurate data collection and clear definitions of opportunities are essential for effective implementation.
Now that you have a comprehensive understanding of DPMO, it’s time to put this knowledge into action. Start by analyzing your processes, calculating DPMO, and identifying areas for improvement. Share your thoughts or experiences in the comments below, and don’t forget to explore other articles on quality management to continue your learning journey!
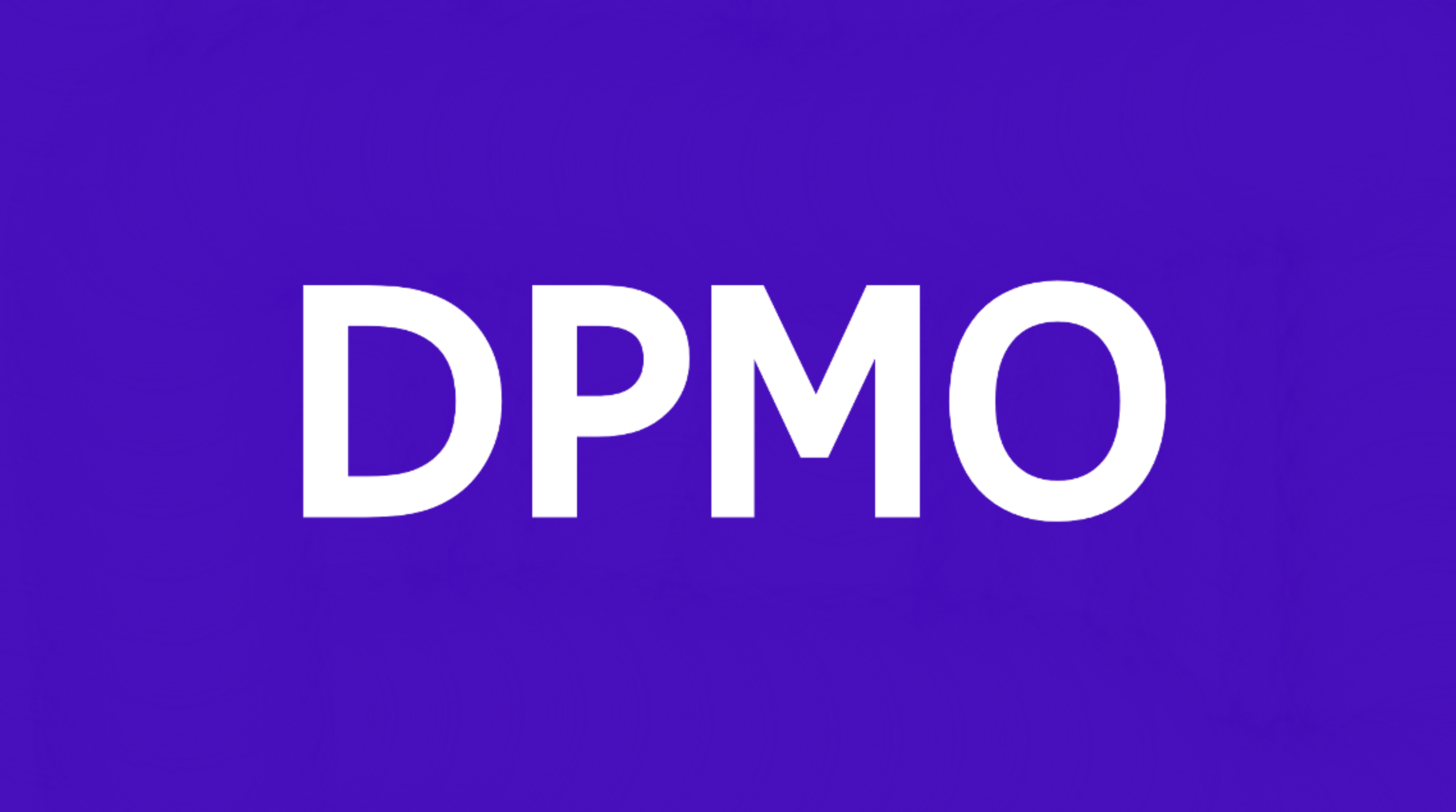
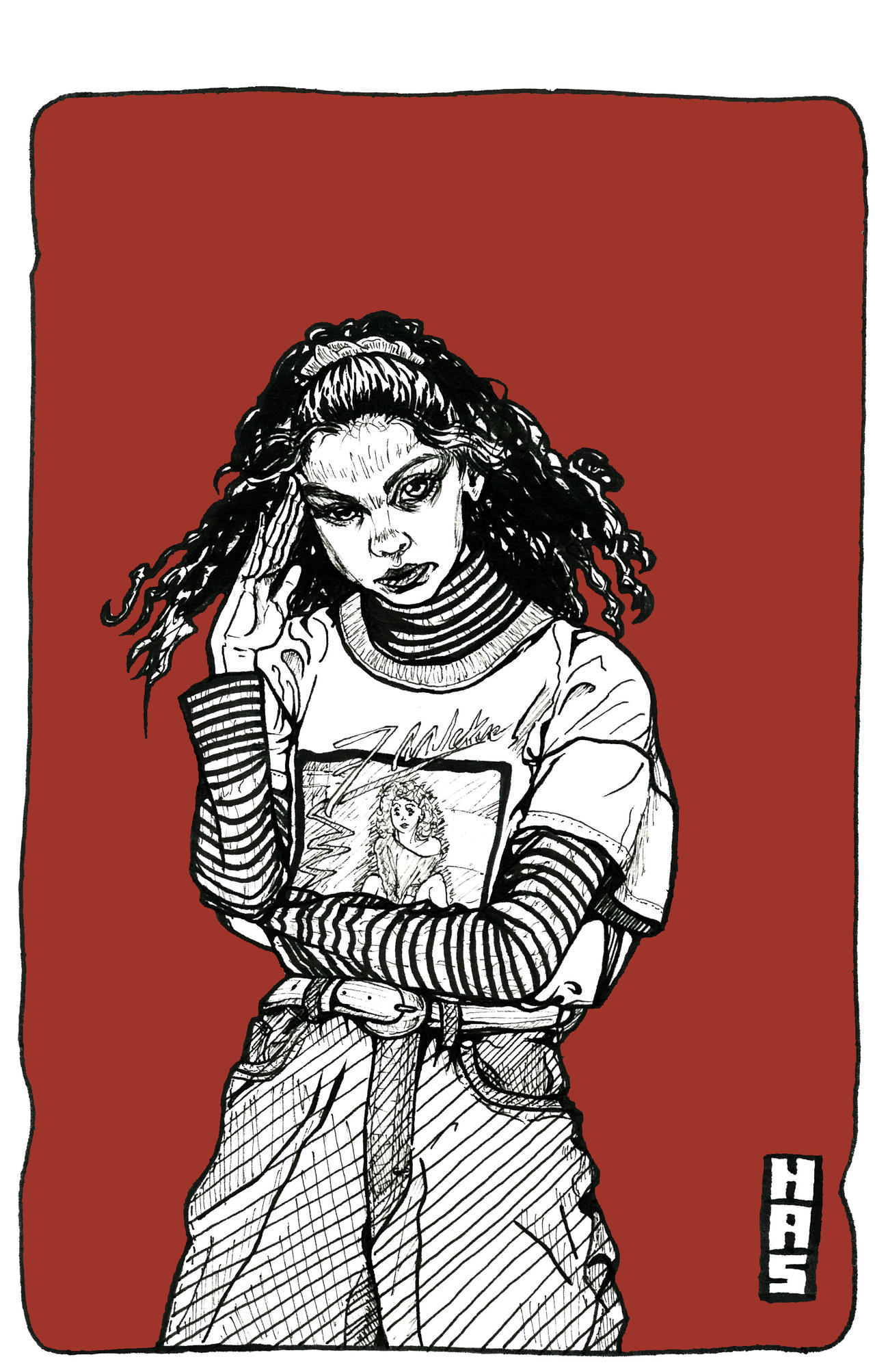