Have you ever wondered what happens when a "bad batch" of products or services reaches the market? Whether it’s a defective batch of electronics, a spoiled shipment of food, or even a poorly executed project, the repercussions can ripple far and wide. A "bad batch" is more than just an inconvenience—it can damage reputations, disrupt industries, and even endanger lives. This issue isn’t confined to one sector; it spans manufacturing, agriculture, pharmaceuticals, and beyond. Understanding what constitutes a bad batch and how to manage it is crucial for businesses and consumers alike.
While the term "bad batch" might sound simple, its implications are complex and multifaceted. Imagine a factory producing thousands of units, only to discover that a small percentage doesn’t meet quality standards. This could lead to costly recalls, customer dissatisfaction, and even legal consequences. Similarly, in the digital world, a "bad batch" of software updates can disrupt workflows and create security vulnerabilities. The stakes are high, and the need for vigilance is even higher. By exploring the origins, consequences, and solutions to bad batches, we can mitigate risks and improve outcomes.
In this article, we’ll delve deep into what defines a bad batch, why it happens, and how it can be prevented or addressed. From examining real-world examples to offering actionable strategies, this guide will equip you with the knowledge to navigate this pervasive issue. Whether you're a business owner, a consumer, or simply someone curious about quality control, this article will provide valuable insights to help you understand and tackle the challenges posed by bad batches.
Read also:Rachel Zegler Snapchat Everything You Need To Know
Table of Contents
- What Exactly Is a Bad Batch?
- Why Does a Bad Batch Happen?
- How Can a Bad Batch Impact Businesses?
- What Are the Real-World Consequences of a Bad Batch?
- How Can You Identify a Bad Batch?
- What Are the Best Practices for Preventing a Bad Batch?
- How Can Businesses Recover from a Bad Batch?
- FAQs About Bad Batches
What Exactly Is a Bad Batch?
A "bad batch" refers to a group of products, services, or outputs that fail to meet predefined quality, safety, or performance standards. This term is widely used across industries, from manufacturing and agriculture to software development and pharmaceuticals. A bad batch can occur due to errors in production, faulty raw materials, or even human oversight. Regardless of the cause, the presence of a bad batch signals a breakdown in quality control processes.
For instance, in the food industry, a bad batch might involve contaminated products that pose health risks to consumers. In manufacturing, it could mean defective parts that compromise the safety of an entire product line. Even in the digital realm, a bad batch of software updates can lead to system crashes or security vulnerabilities. The common thread across these scenarios is the deviation from expected standards, which can have far-reaching consequences.
Key Characteristics of a Bad Batch
Identifying a bad batch involves recognizing specific characteristics that set it apart from acceptable outputs. Here are some key indicators:
- Consistency Issues: Products in a bad batch often exhibit inconsistencies in quality, size, or performance.
- Performance Failures: Items may fail to function as intended, leading to customer complaints or returns.
- Safety Concerns: A bad batch can pose risks to users, whether through physical harm or data breaches.
- Regulatory Non-Compliance: Products that don’t meet industry regulations or standards are often classified as part of a bad batch.
Why Does a Bad Batch Happen?
Understanding the root causes of a bad batch is essential for preventing future occurrences. While the specific reasons may vary depending on the industry, several common factors contribute to the emergence of a bad batch. These include human error, equipment malfunctions, and supply chain disruptions.
Human Error: The Silent Culprit
Human error is one of the leading causes of a bad batch. Whether it’s a mistake in programming, miscommunication during production, or oversight in quality checks, even small errors can lead to significant problems. For example, a worker might accidentally use the wrong raw material, or a manager might fail to catch a critical flaw during inspections. These errors often go unnoticed until the product reaches the consumer, at which point the damage is already done.
Equipment Malfunctions and Maintenance Issues
Another major factor is equipment malfunction. Machines used in production are prone to wear and tear, and if they aren’t properly maintained, they can produce substandard outputs. For instance, a faulty conveyor belt might mishandle products, leading to physical damage. Similarly, outdated software systems can generate errors that result in a bad batch of digital outputs. Regular maintenance and upgrades are crucial to minimizing these risks.
Read also:What Does Mmcht Mean A Comprehensive Guide To Understanding This Acronym
Supply Chain Disruptions
Supply chain issues can also contribute to the creation of a bad batch. Delays in receiving raw materials, unexpected shortages, or reliance on low-quality suppliers can all lead to subpar outputs. For example, a sudden spike in demand might force a company to cut corners, resulting in compromised quality. Managing supply chain risks is therefore a key component of preventing bad batches.
How Can a Bad Batch Impact Businesses?
The impact of a bad batch on businesses can be both immediate and long-lasting. From financial losses to reputational damage, the consequences are significant and multifaceted. Companies that fail to address these issues promptly risk losing customer trust and market share.
Financial Implications
One of the most obvious impacts of a bad batch is the financial cost. Recalls, refunds, and legal fees can quickly add up, straining a company’s resources. For example, a food company might have to recall an entire shipment of contaminated products, incurring costs for logistics, disposal, and compensation. Similarly, a tech company might face lawsuits if a bad batch of software updates leads to data breaches or system failures.
Reputational Damage
Beyond the financial toll, a bad batch can severely damage a company’s reputation. Consumers expect high-quality products and services, and a single misstep can erode trust. Negative reviews, social media backlash, and media coverage can amplify the impact, making it difficult for businesses to recover. Rebuilding trust takes time and effort, and some companies may never fully regain their footing.
Operational Disruptions
Operational disruptions are another consequence of a bad batch. For instance, a manufacturing plant might have to halt production to address quality issues, leading to delays and lost revenue. Similarly, a software company might need to divert resources to fix bugs, slowing down other projects. These disruptions can have a cascading effect, impacting everything from employee morale to customer satisfaction.
What Are the Real-World Consequences of a Bad Batch?
To truly understand the gravity of a bad batch, it’s helpful to examine real-world examples. These case studies highlight the far-reaching consequences of quality control failures and underscore the importance of vigilance.
The Peanut Corporation of America Recall
In 2008, the Peanut Corporation of America faced one of the largest food recalls in U.S. history due to a bad batch of contaminated peanut butter. The contamination led to a nationwide salmonella outbreak, resulting in multiple deaths and hundreds of illnesses. The company eventually filed for bankruptcy, and its executives faced criminal charges. This case serves as a stark reminder of the human cost of a bad batch.
The Boeing 737 MAX Crisis
The Boeing 737 MAX crisis is another example of how a bad batch can have devastating consequences. Faulty sensors and software issues led to two tragic crashes, claiming hundreds of lives. The fallout included global grounding of the aircraft, billions in financial losses, and a tarnished reputation for one of the world’s leading aerospace companies. This incident underscores the importance of rigorous testing and quality assurance.
Lessons Learned
These examples highlight the importance of proactive measures to prevent bad batches. From implementing robust quality control systems to fostering a culture of accountability, businesses must take steps to mitigate risks. The lessons learned from these crises can serve as a blueprint for avoiding similar pitfalls in the future.
How Can You Identify a Bad Batch?
Early identification of a bad batch is crucial for minimizing its impact. By implementing effective monitoring and testing protocols, businesses can catch issues before they escalate. Here are some strategies for identifying a bad batch:
Quality Control Checks
Regular quality control checks are the first line of defense against bad batches. These checks involve inspecting products at various stages of production to ensure they meet standards. For example, a food company might test samples for contamination, while a tech company might run diagnostic tests on software updates.
Customer Feedback
Customer feedback is another valuable tool for identifying bad batches. Complaints, returns, and reviews can provide early warning signs of quality issues. By actively monitoring feedback channels, businesses can address problems before they spiral out of control.
Data Analytics
Advancements in data analytics have made it easier to detect anomalies in production. By analyzing data from sensors, machines, and customer interactions, companies can identify patterns that indicate a bad batch. For example, a sudden spike in defect rates might signal an underlying issue that needs to be addressed.
What Are the Best Practices for Preventing a Bad Batch?
Prevention is always better than cure, and this holds true for bad batches. By adopting best practices, businesses can significantly reduce the risk of quality control failures. Here are some strategies to consider:
Invest in Training and Development
Human error is a leading cause of bad batches, so investing in employee training is essential. By educating workers on quality standards and procedures, businesses can minimize mistakes. Regular workshops, certifications, and refresher courses can help reinforce best practices.
Upgrade Equipment and Technology
Outdated equipment is a common culprit behind bad batches. Upgrading machinery and technology can improve accuracy and efficiency, reducing the likelihood of errors. For example, automated systems can perform tasks with greater precision than manual processes, leading to higher-quality outputs.
Strengthen Supply Chain Management
A robust supply chain is critical for preventing bad batches. By working closely with suppliers and implementing stringent quality checks, businesses can ensure they receive reliable raw materials. Diversifying suppliers and maintaining buffer stocks can also help mitigate risks.
How Can Businesses Recover from a Bad Batch?
Recovering from a bad batch requires a strategic approach. From issuing recalls to rebuilding trust, businesses must take decisive action to mitigate the damage. Here are some steps to consider:
Transparent Communication
Transparency is key to rebuilding trust after a bad batch. Businesses should communicate openly with customers, explaining the issue and outlining the steps being taken to address it. Issuing public apologies and providing updates can go a long way in restoring confidence.
Implementing Corrective Measures
Corrective measures are essential for preventing future occurrences. This might involve revising production processes, upgrading equipment, or retraining employees. By addressing the root cause of the issue, businesses can reduce the risk of a repeat incident.
Compensating Affected Customers
Compensation can help ease the burden on affected customers and demonstrate a commitment to accountability. Whether it’s offering refunds, replacements, or discounts, businesses should prioritize customer satisfaction during the recovery process.
FAQs About Bad Batches
What Should I Do If I Receive a Bad Batch?
If you receive a bad batch, the first step is to document the issue. Take photos, gather evidence, and contact the supplier or manufacturer immediately. Request a replacement or refund, and follow up to ensure the issue is resolved.
How Can I Prevent a Bad Batch in My Business?
Preventing a bad batch involves implementing robust quality control measures, investing in employee training, and upgrading equipment. Regular audits and feedback loops can also help identify potential issues before they escalate.
What Are the Legal Implications of a Bad Batch?
The legal implications of

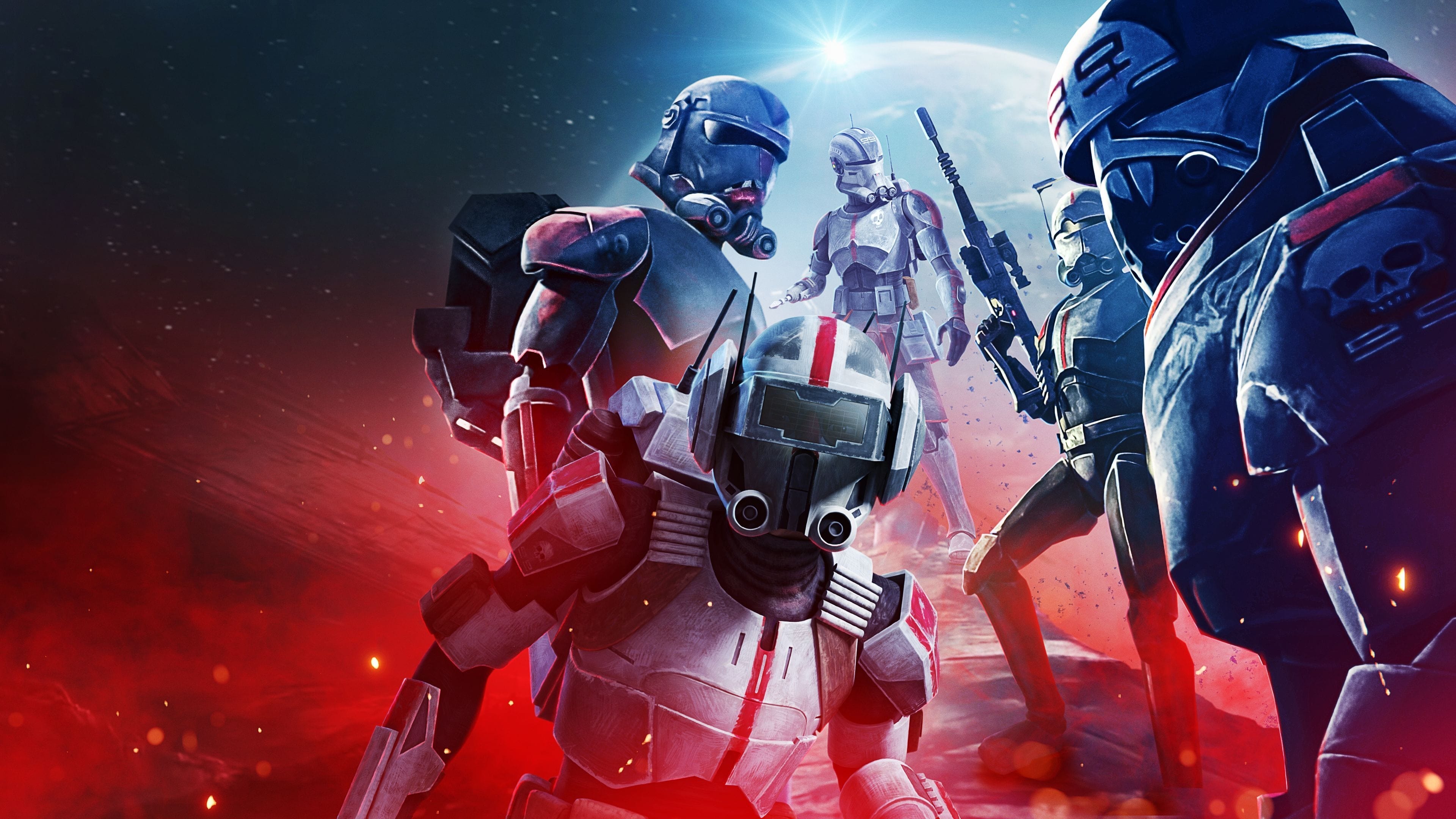